In March 2020, the UK was on the cusp of the first national lockdown and the Four Nations Public Health HCID Group had made an interim recommendation to classify COVID-19 as a High Consequence Infectious Disease (HCID).
As London Hospitals were quickly becoming overwhelmed by admissions of COVID-19 patients, Norwich University Hospital (NNUH) had been designated as one of a number of “surge centres” to accommodate patients who required critical care. At the time, Negative Pressure Isolation Facilities were incredibly rare in the UK with only 15 beds across 4 hospitals.
These unique facilities are primarily designed to treat patients with HCID diseases such as Ebola, SARS, MERS, Hantavirus, Avian Influenza but with the spread of COVID-19 accelerating, NNUH were looking to get working facilities in place in just 8 weeks, which in their own words, ‘simply didn’t seem possible’.

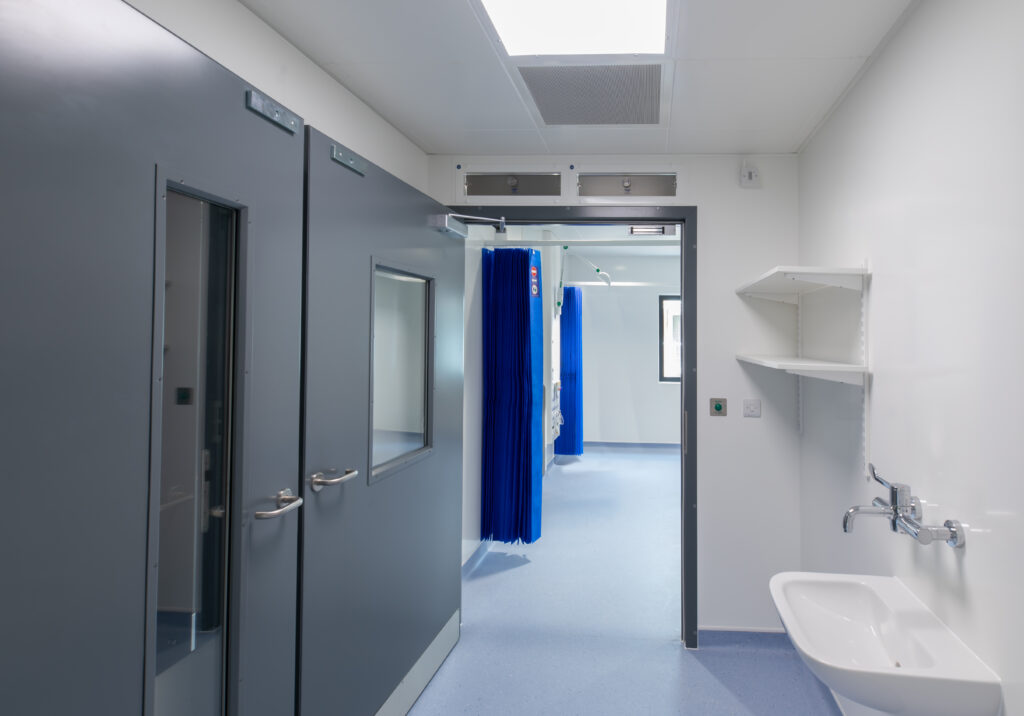
In addition to the rarity of the design, the location of the units also promised to be a significant challenge. Most hospitals have ‘Green’ and ‘Red’ zones to indicate where COVID patients are being treated and the ‘Red zones’ available to accommodate the new facilities consisted of an array of steep banks and 45 degree-cut-down-dips – all which would have required months of traditional construction to build the foundations required.
The challenge presented to ModuleCo, together with the nationwide situation, was daunting. We had just 8 weeks to design, build and deliver a Negative Pressure Isolation Facility, capable of accommodating HCID patients, on a site not ready to be built upon, in the middle of a pandemic which was rapidly sweeping the country.
From the Monday when we committed to the 8 week programme, the ModuleCo design team had created and submitted the electrical and mechanical design from scratch by the Wednesday of the same week.
Knowing that NNUH faced both practical and time issues which had hindered the possibility of a traditional foundation, we opted to use our ‘Dynamic Load Technology’.
It is technology which allows us to build in almost any location without having to prepare large foundations – we asked the NNUH to position some plinths for us to place the pads onto, which provided a solid foundation for the modules to be placed upon.


This is another great example of why off-site construction can dramatically change and benefit the outcome of a project. We took an issue which could have potentially taken months to correct and instead, built the pads in the factory, sat the Negative Pressure Isolation Units on top and ‘stress-tested’ them – three days after they were tested, they arrived at NNUH, signed off, QA approved and available to use.
With every day critical to meeting the agreed timescales, ModuleCo’s designs had to be ‘right first time’ and this required clear and accurate communication across our respective project teams as well as fast-paced decision making and sign off by the Trust.
From agreeing the design to the first modules arriving on site took just 41 days and during this time preparatory works had to be completed on site to ensure module installation could proceed seamlessly as planned.
With 90% of the work completed in our factory, once on site, the Trust only needed to provide power, potable water and medical gas services – vastly reducing the impact to the estate and allowing for rapid connections to be made.
A week of final connections and commissioning took place before the facility was handed over to Trust for occupation during week 8 of the programme.

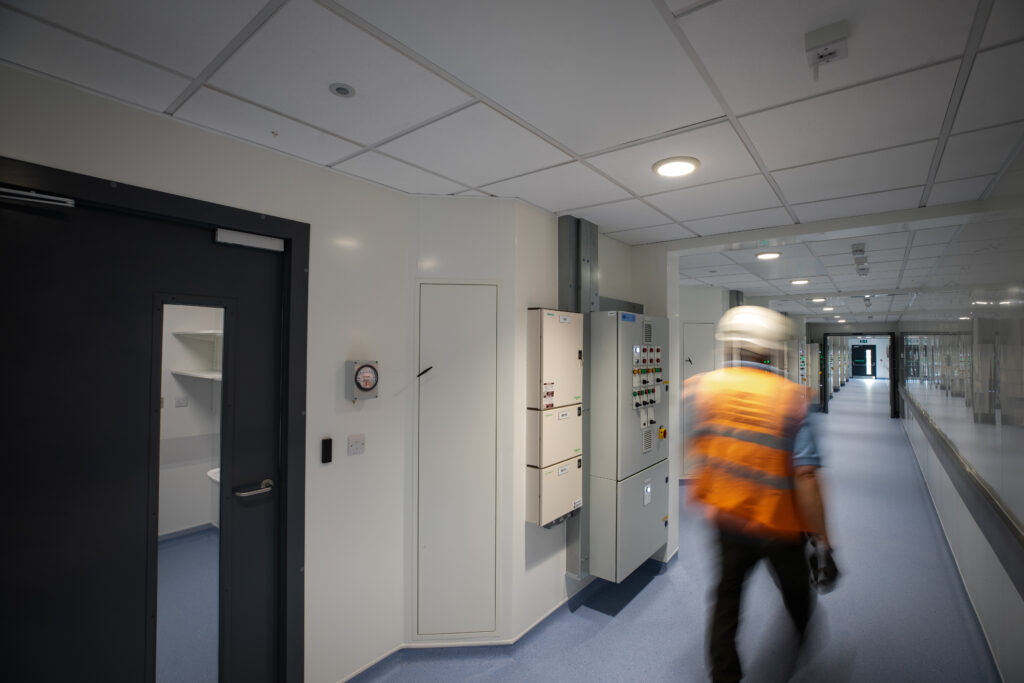
Under normal circumstances, the complexity of HCID facilities represent a unique challenge, the location potentially rendered the project unachievable and the circumstances presented by the pandemic, were unpredictable, at best.
From the moment we agreed on a path forward, the team at ModuleCo researched, developed and built all of the components entirely in-house to ensure that the NNUH could fulfil their promise to accommodate and facilitate the surge requirements presented by COVID-19.
The 6,700ft2 standalone Isolation Ward offers 10 single occupancy, en-suite rooms alongside ancillary support spaces for the clinical and nursing staff.
Designed to meet the specifications for HCID units, each patient room is supported by its own independent ventilation plant and safe change HEPA filter extract unit.
Each room has its own dedicated AHU providing a minimum of 10 air changes per hour and is coupled with a negative pressure regime that is protected by a ventilated entrance lobby.
In each lobby the dedicated supply/extract is mechanically interlocked to ensure there is no risk of a positive pressure regime arising should there be an AHU failure.
Two weeks after the project was delivered, alongside a similar requirement in Cardiff, we had more than doubled the UK’s HCID capacity from 15 to 35 beds. And, by using off-site construction, we were able to do this with minimal disruption.
In partnership with the team at NNUH, these facilities allow health professionals to provide critically ill patients with the necessary conditions for a faster and successful recovery, which is something that we take immense pride in as a team.